What is considered high-nickel alloy steel?
Before we explore what is considered high-nickel alloy steel, let’s analyse the properties of nickel in more detail.
Nickel has amazing physical and chemical properties, which make it essential in hundreds of thousands of products. Nickel’s most common use is alloying – particularly with chromium and other metals to produce stainless and heat-resistance steels.
Properties of Nickel
- Nickel has a high melting point of 1453 °C.
- It is resistant to corrosion and oxidation.
- A hard substance but is highly malleable and ductile.
- Nickel alloys readily, as we will explore in more detail below.
- It is magnetic at room temperature.
- Can be deposited by electroplating (coat a thin layer of nickel onto metal by electrolytic deposition).
- It has catalytic properties (can increase the speed of a chemical reaction).
- Nickel is fully recyclable – nickel can be recycled again and again without loss of quality, contributing to the Circular Economy (CE) model.
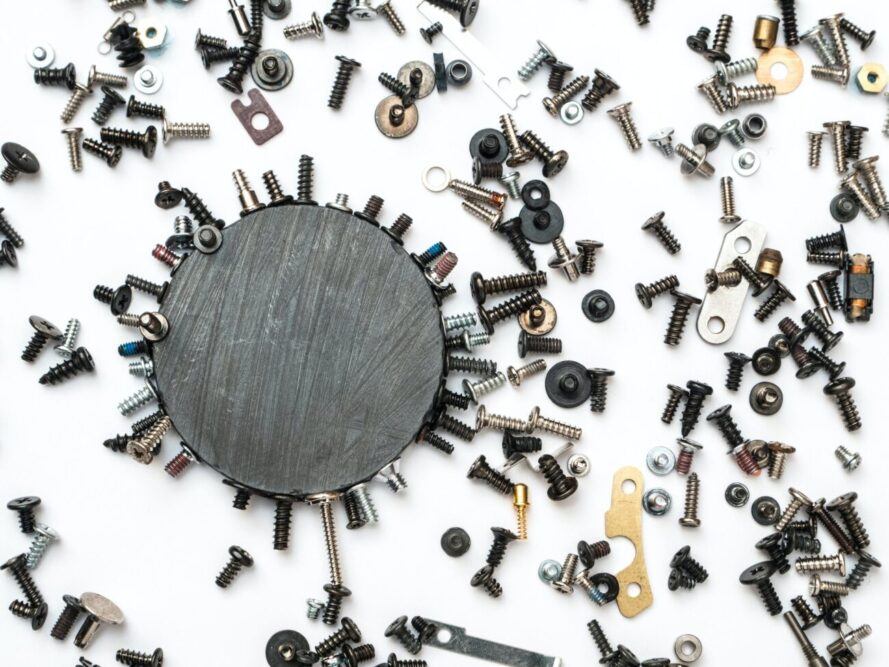
What is the Purpose of Nickel Alloy Steels?
Alloy steels with high-nickel content are a mix of steel with a particular chemical composition that makes them optimal at high temperatures and in corrosive and oxidizing environments.
Nickel within an alloy offers many advantages which do not affect the deformability of the steel.
Typically, these alloys, with different percentages of nickel, allow the reduction of the annealing and quenching temperatures that, in addition to the critical speed, create a greater hardening penetration. Finally, these alloys upgrade the strength of the components.
Alloy steels include a wide variety of iron-based materials. Nickel content ranges from very low, ~0.3% in some alloy steels, and up to as much as 20% in maraging steels.
The amount of nickel in each alloy is designed to create the perfect combination of strength, hardness, wear resistance, or toughness for its purpose than what plain-carbon steels can provide. They are generally used in equipment that delivers power, forms, and cuts metal, or are used at low temperatures where carbon steels lack adequate toughness.
Nickel alloy steels are essential in the construction of tools and machinery that enable industries to make other tools and machinery.
What Constitutes as High-Nickel Alloy Steel?
High nickel alloys containing 25% to 65% Ni are the most resistant to both CO2 and H2S corrosion. No limits are given for CO2 corrosion, whereas H2S corrosion is a function of the nickel content. Inconel alloys, like UNS N08825 and UNS N06625, are the most widely used high-nickel alloys in the oil industry.
However, there is no precise minimum for what constitutes high-nickel alloy steel. Some sources would claim at least 25% NI, others suggest anything above 3% is a high-nickel alloy. It all depends on what purpose you need the alloy to fulfil in order to decide what would constitute high-nickel alloy steel.
In carbon and most low-alloy steels, as the temperature drops below 24 °C, strength and hardness increase, while tensile ductility and toughness decrease. Nickel improves low-temperature toughness. Although still classified as high-nickel alloys, steel alloys containing greater than 3% nickel are high enough to withstand cold regions.
For example, ferritic steels with more than 3% high-nickel content have extensive use in applications involving exposure to temperatures from 0 °C to -196 °C. Such applications include storage tanks for liquefied hydrocarbon gases, as well as structures and machinery designed for use in cold regions.
These steels utilise the effect of nickel content in reducing the impact transition temperature, thereby improving toughness at low temperatures. Thus, steel alloys containing more than 3% nickel would be high content for the purposes mentioned above, but perhaps not enough nickel for alloys in the oil industry.
Nickel Alloys We Sell
Check out what nickel alloys we sell!
If you are unsure what percentage of nickel is needed for your high-nickel alloy steels, head over to our Contact page so that our in-house Metallurgist can help you out!
Leave a comment